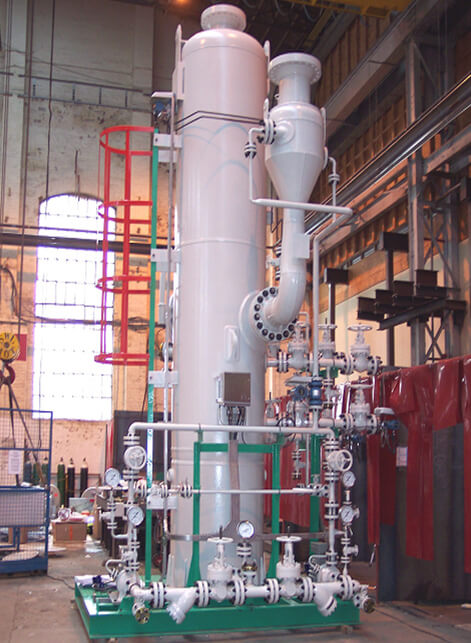
Venturi Scrubbers
Venturi scrubbers are used for solids removal from flue gases and process vents, providing efficient removal of particulates as small as 0.2 µm (micron). The scrubbers are suitable for mechanically generated (large) and chemically generated (small) particulates with typical particulate size in the range 0.5 to 10 µm. Material loading, density, and solubility are all factored into ERG’s design.Venturi Operating Principle The flue or process vent gas stream enters the top of the venturi where the scrubbing liquid (usually recirculated) is sprayed into the gas stream. In the venturi throat, the gas accelerates and mixes intimately with the scrubbing liquid due to the intense eddies present in the turbulent flow. The change in momentum allows the particulate to be entrained in the liquid droplets, effectively removing the solids from the gas stream. The droplets then recombine as the gas slows and expands at the venturi outlet, agglomerating in the cyclone separator and draining into the sump tank ready for recirculation through the venturi throat. A final mist elimination stage removes any residual droplets. Venturis may be orientated vertically, horizontally or at an angle.
Venturi Selection
The gas pressure drop determines the particulate removal efficiency. The smaller the particulate, the larger the pressure drop required. Indicative performance is shown in the graph below: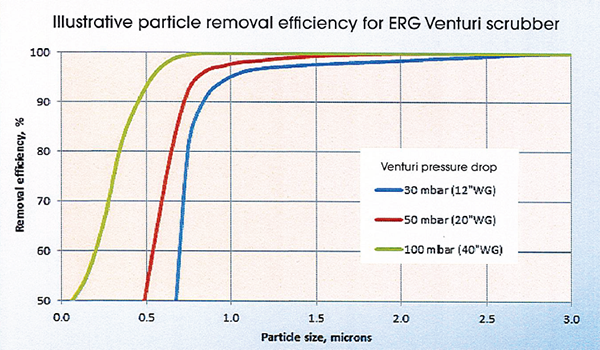
Fixed throat venturis have no internal moving parts and so are simple to operate and maintain. If the gas flow rate is variable, the pressure drop across the throat varies and so does the particulate removal efficiency. Higher flow rates result in greater particulate removal efficiency.
Variable throat venturis include adjustable blades in the throat. For variable gas flows these can be automatically modulated to achieve a constant pressure drop ensuring high and consistent particulate removal efficiency is maintained, independent of flowrate. The mechanism that adjusts the position of the blades is located outside the gas flow and is highly reliable. Variable throat venturis may also be manually adjustable to optimise performance and power consumption without the complexity of an automatic actuator and control loop.
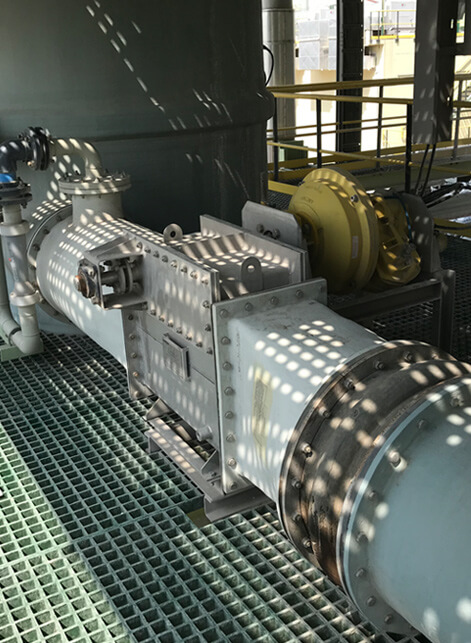
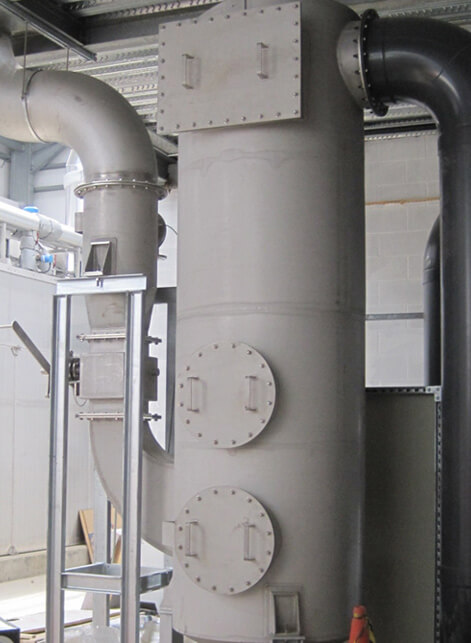
System Configuration Options
ERG venturi scrubbers are typically supplied as part of a gas cleaning package. The package is designed for each application, and can include:- Side stream settler and/or press – used with insoluble particulate to remove the captured solids from the liquor circuit as a slurry or a dry cake.
- Separate sump tank – used to allow on-line inspection of the scrubbing liquor, especially when the particulate is prone to float on the liquid surface.
- Integrated quench and venturi vessel – used when hot flue gas is being treated. The gas is quenched to the adiabatic saturation temperature in the upper part of the venturi and then accelerated in the throat below.
- High pressure fans – to provide the motive force through the system extraction ducts, venturi vessel and any additional scrubbing stages. Treated gas is discharged to the client’s process or to atmosphere. Typical fan duties range from 25 to 100 mbar depending on the application.
- Recirculation pumps – pumps with suitable seal plan provide the required flow rate and pressure at the venturi throat. Enhanced system reliability and availability is achieved by using a duty/standby arrangement.
- Down-stream scrubbing – is frequently required to remove soluble acidic (e.g. HCI, CI2, HF, HBr, SO2) or alkaline (e.g. NH3) contamination. This is provided by other ERG mass transfer technologies, e.g. packed towers, V-Tex® scrubbers or tray towers.
Construction Materials
Depending on the operating temperature, gas composition and contaminant type, ERG can provide the venturi and cyclone in carbon or stainless (304, 316) steels, duplex, Hastelloy (C22 or C276), Inconel, or PVC/GRP, PP/GRP or chemically resistant GRP (Crystic® or Derakane® resins).Venturi Scrubbers
Venturi scrubbers are used for solids removal from flue gases and process vents, providing efficient removal of particulates as small as 0.2 µm (micron). The scrubbers are suitable for mechanically generated (large) and chemically generated (small) particulates with typical particulate size in the range 0.5 to 10 µm. Material loading, density, and solubility are all factored into ERG’s design.Venturi Operating Principle The flue or process vent gas stream enters the top of the venturi where the scrubbing liquid (usually recirculated) is sprayed into the gas stream. In the venturi throat, the gas accelerates and mixes intimately with the scrubbing liquid due to the intense eddies present in the turbulent flow. The change in momentum allows the particulate to be entrained in the liquid droplets, effectively removing the solids from the gas stream. The droplets then recombine as the gas slows and expands at the venturi outlet, agglomerating in the cyclone separator and draining into the sump tank ready for recirculation through the venturi throat. A final mist elimination stage removes any residual droplets. Venturis may be orientated vertically, horizontally or at an angle.
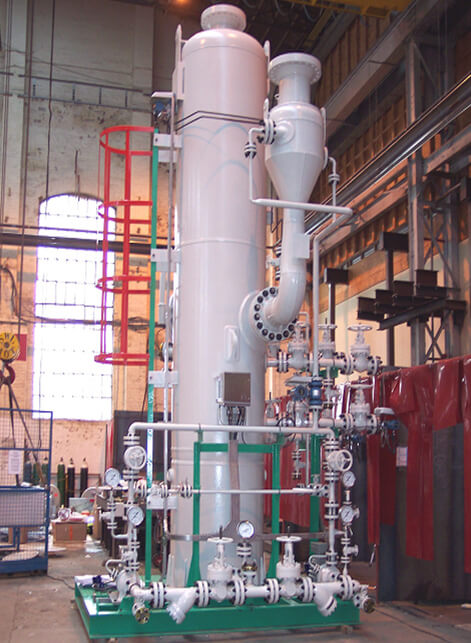
Venturi Selection
The gas pressure drop determines the particulate removal efficiency. The smaller the particulate, the larger the pressure drop required. Indicative performance is shown in the graph below: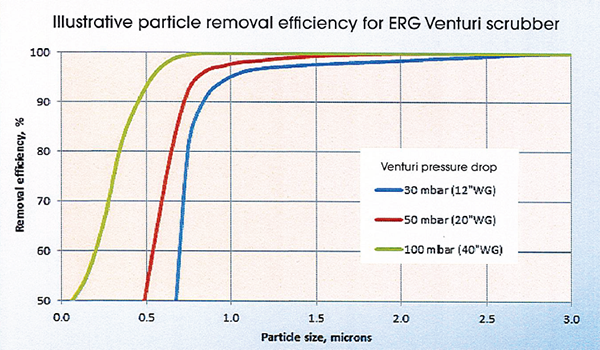
Fixed throat venturis have no internal moving parts and so are simple to operate and maintain. If the gas flow rate is variable, the pressure drop across the throat varies and so does the particulate removal efficiency. Higher flow rates result in greater particulate removal efficiency.
Variable throat venturis include adjustable blades in the throat. For variable gas flows these can be automatically modulated to achieve a constant pressure drop ensuring high and consistent particulate removal efficiency is maintained, independent of flowrate. The mechanism that adjusts the position of the blades is located outside the gas flow and is highly reliable. Variable throat venturis may also be manually adjustable to optimise performance and power consumption without the complexity of an automatic actuator and control loop.
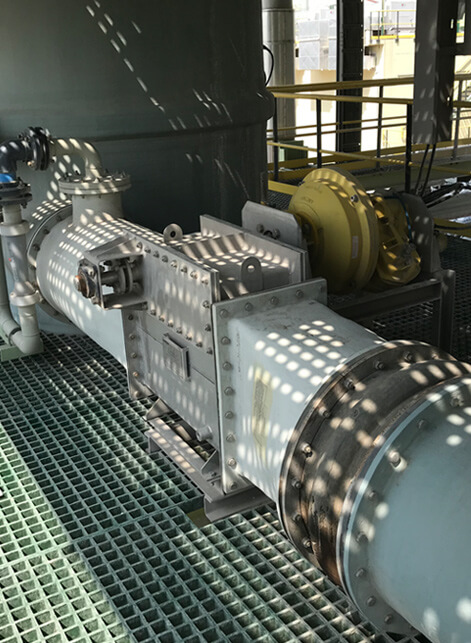
System Configuration Options
ERG venturi scrubbers are typically supplied as part of a gas cleaning package. The package is designed for each application, and can include:- Side stream settler and/or press – used with insoluble particulate to remove the captured solids from the liquor circuit as a slurry or a dry cake.
- Separate sump tank – used to allow on-line inspection of the scrubbing liquor, especially when the particulate is prone to float on the liquid surface.
- Integrated quench and venturi vessel – used when hot flue gas is being treated. The gas is quenched to the adiabatic saturation temperature in the upper part of the venturi and then accelerated in the throat below.
- High pressure fans – to provide the motive force through the system extraction ducts, venturi vessel and any additional scrubbing stages. Treated gas is discharged to the client’s process or to atmosphere. Typical fan duties range from 25 to 100 mbar depending on the application.
- Recirculation pumps – pumps with suitable seal plan provide the required flow rate and pressure at the venturi throat. Enhanced system reliability and availability is achieved by using a duty/standby arrangement.
- Down-stream scrubbing – is frequently required to remove soluble acidic (e.g. HCI, CI2, HF, HBr, SO2) or alkaline (e.g. NH3) contamination. This is provided by other ERG mass transfer technologies, e.g. packed towers, V-Tex® scrubbers or tray towers.
Construction Materials
Depending on the operating temperature, gas composition and contaminant type, ERG can provide the venturi and cyclone in carbon or stainless (304, 316) steels, duplex, Hastelloy (C22 or C276), Inconel, or PVC/GRP, PP/GRP or chemically resistant GRP (Crystic® or Derakane® resins).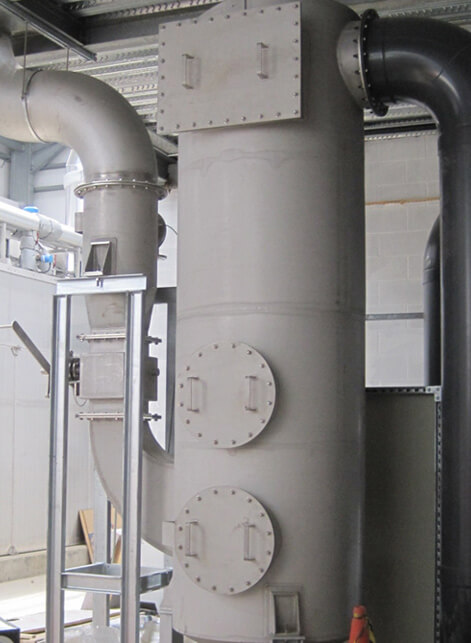