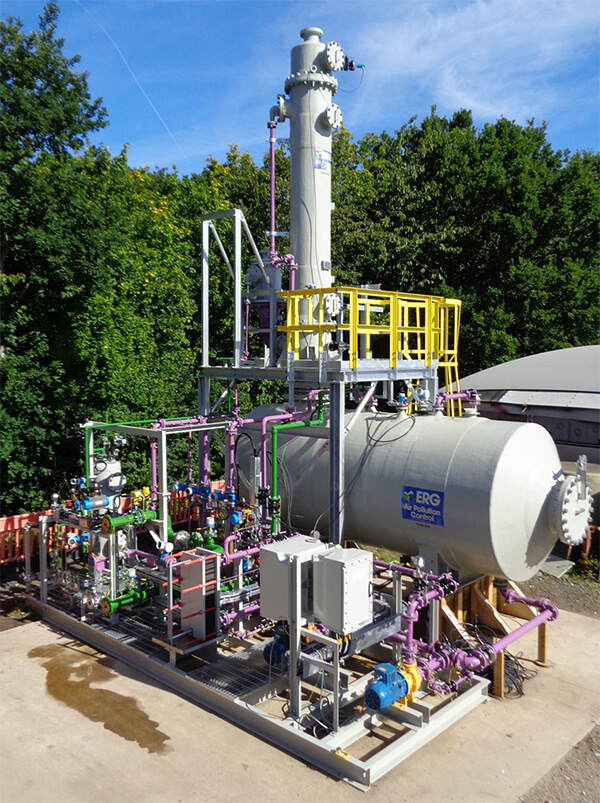
Chemical Plant Air Pollution Treatment
ERG provides a wide variety of air pollution control systems for Chemical production plants. ERG’s purpose-designed scrubbing systems are engineered to suit each application and client’s requirements and are supplied with a process guarantee.
We have reference plants throughout the chemical industry, with sector experience in bulk chemicals, fertilisers, intermediates, fine chemicals, agrochemicals, heat-resistant materials manufacture, speciality chemicals, petrochem and consumer products.
Applications
ERG’s abatement packages are typically installed to treat vents from storage tanks, reactors, vent lines/LEV systems, liquid waste handling, packaging areas and thermal oxidisers. In many cases, a skid-mounted scrubber package is required, though ERG can also arrange site installation and commissioning.
Typical contaminants which we treat include:
- Acid gases – HCl, Cl2, Br2, COS, HCN, SO2, H2S, mercaptans, etc
- Basic gases – NH3, amines, etc
- Silicates – SiO2, H2SiF6, SiF4, SiCl4, etc
- Dust and aerosols – 100 to <1 micron particle sizes – mechanically and chemically generated dust including catalysts, zeolites, PTA, rubber
- VOCs – MEK, methyl chloride, THF, ethyl acetate, acetone, etc
ERG has particular experience treating halogenated semi-metals (BCl3, SiCl4, SiF4, etc) where difficult to handle gelatinous or solid precipitates form on contact with the scrubbing liquor, leading to potential for system blockage.
Download our studies to read further.
Technologies
Our vent abatement systems are based on one or more of the following technologies. Each package is bespoke: designed and manufactured to the specific project requirements.
- Packed tower scrubbers – for acid gases, basic gases, some dusts, some VOCs
- V-tex® scrubbers – for acid gases, basic gases, some dusts, some VOCs VOCs, and especially suitable to gelatinous hydrolysis products
- Venturi scrubbers – for high concentration or fine dust
- Carbon filters – for VOCs and solvent abatement
- Quench systems – for adiabatically cooling high temperature gas for further wet scrubbing
- Tray scrubbers – typically large flowrate low concentration gases and dusts
- Thermal oxidation – waste solvents and VOC-rich vent gases
- Low temperature DeNOx – for NOx abatement to high efficiency
ERG is skilled at system integration, adding additional abatement techniques from third-party vendors into our systems. Examples include bag filters, ceramic filters, RTOs, SCR/SNCR de-NOx, liquid effluent treatment.
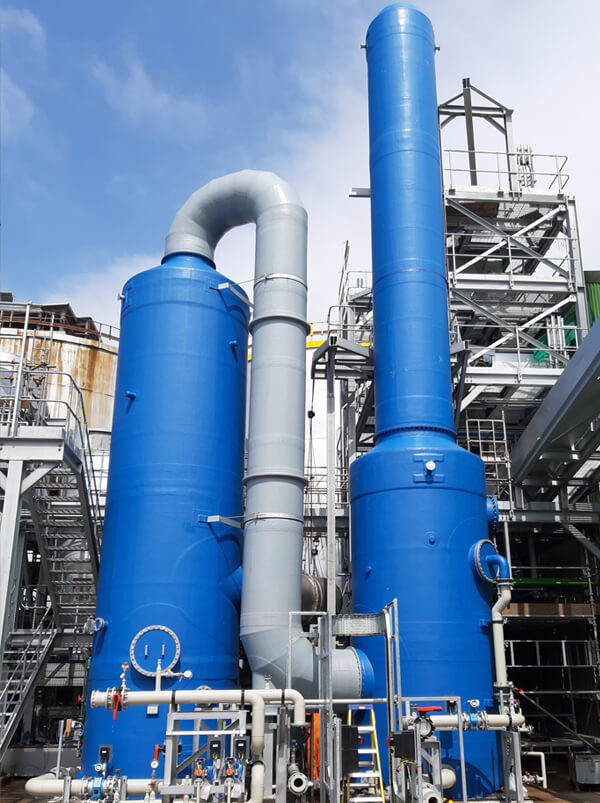
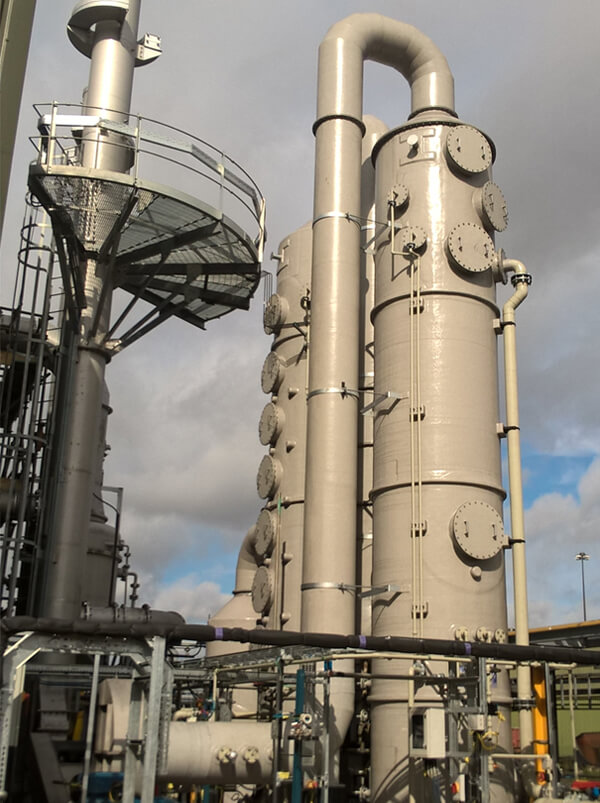
Meeting Exacting Specifications
ERG’s design and project management teams are highly experienced at delivering packaged plant which meets the chemical industry’s needs.
- All design and procurement is managed according to our ISO9001 procedures
- All manufacturing and assembly is to the agreed codes and project specifications, managed through and certified against the project Quality and Inspection & Test Plans.
- All equipment is fully certified and documented in accordance with applicable European Standards, and CE marked accordingly.
- Vessels can be supplied to BS EN 13121, PD 5500 or ASME VIII as appropriate, and packages CE marked to the Pressure Equipment (2014/68/EU) and ATEX (2014/34/EU) Directives depending on the specification requirements.
- Safety in design and operation is our highest priority. We work with the main contractor, designer and end user to ensure the safety case documentation, HAZOP, etc are conducted thoroughly and efficiently.
Choice of Materials
Every ERG package has materials selected to match the specification. All systems are mechanically designed for the operating and design pressures (typically ambient ±50-100mbarg, though can be from FV to +40barg) and temperatures (ambient upwards to suit the process). Common materials selections are listed below, though alternatives are available to suit the process requirements.
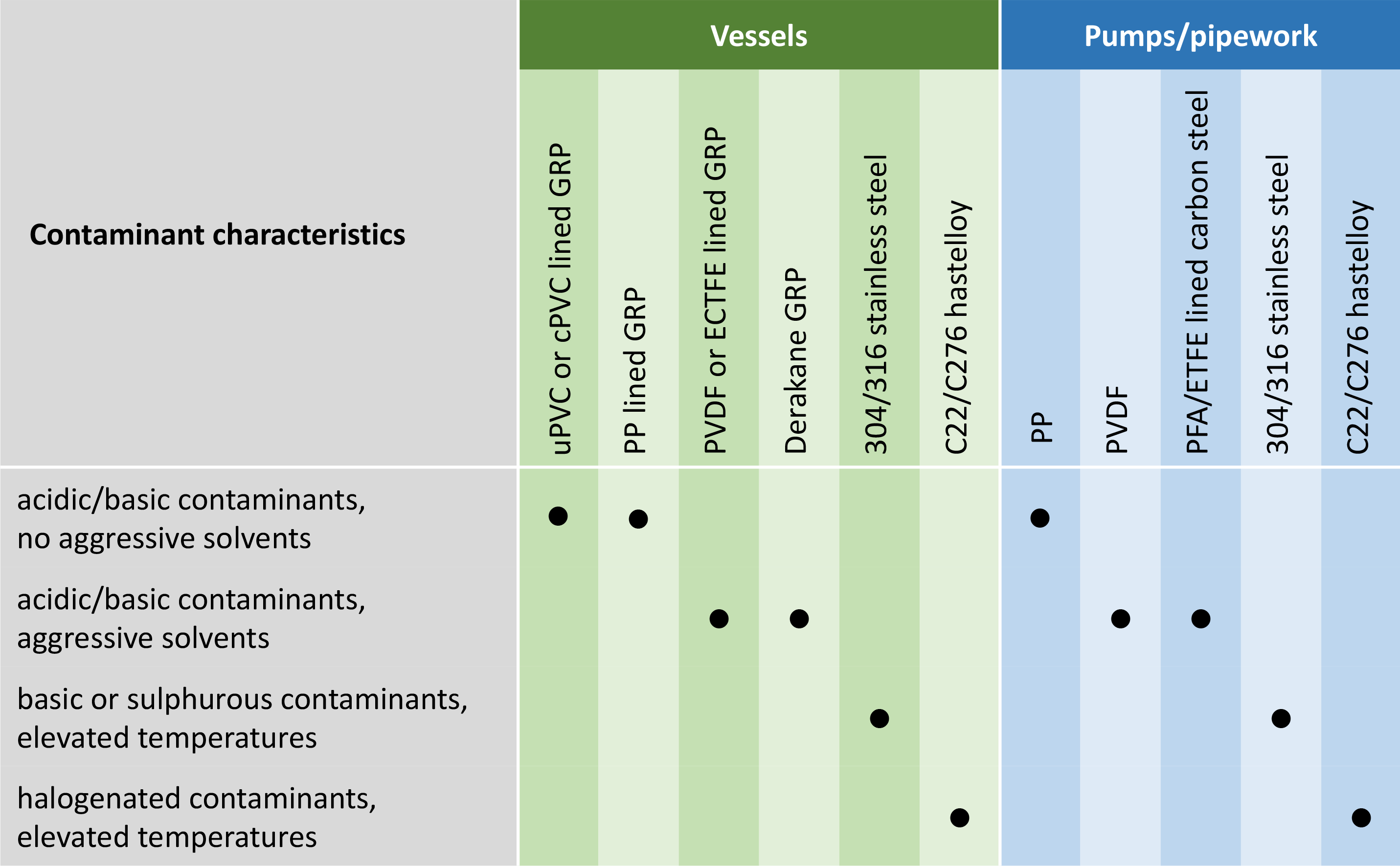
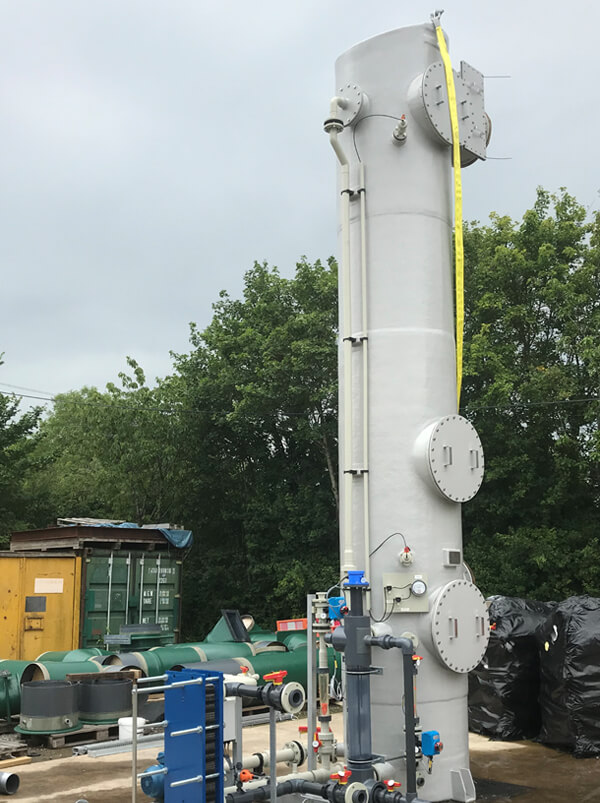
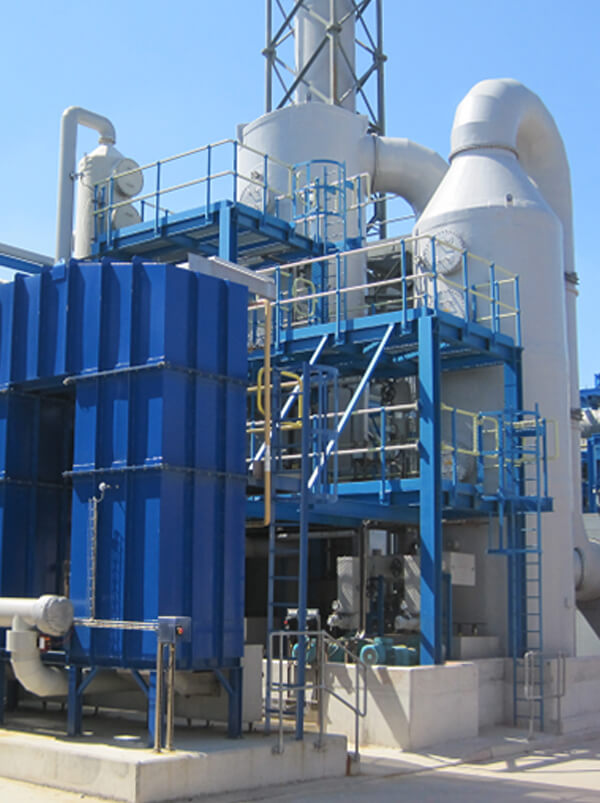
ERG Package Scope of Supply
ERG is a specialised scrubbing supplier. Our typical scope includes:
- Project management including customer design reviews, progress reporting, equipment interface agreement, programme management, site activities co-ordination, documentation packages
- Process design and technical submission – heat & mass balance, P&ID, control philosophy, technical schedules
- Detailed mechanical and electrical design – model and/or package General Arrangement drawings, civils requirements, site wiring details, interface details, off-loading and installation details
- Sub-supplier procurement, quality assurance and expediting – vessels, pipework & valves, pumps, fans, heat exchangers, instrumentation, control panels or local JBs, access steelwork, pressure protection devices
- Package assembly including full pipework and wiring, factory testing, certification
- Delivery
- Installation and commissioning are also available if required – phone support during this phase can be arranged if preferred
Plastic and GRP vessels are manufactured by ERG’s sister company ERG (Plastic Fabrication) Ltd (ergpf.co.uk). Skid assembly and testing are managed at ERG (Plastic Fabrication) Ltd’s facility in West Sussex.
Operational Peace of Mind
- Every ERG abatement package carries a performance guarantee – as an operator you can be sure the equipment will meet the process requirements
- Our standard (12 months) or extended warranty guarantees the mechanical and electrical parts against defects
- And our Maintenance department can assist with routine, shut-down or emergency maintenance
Our Clients
ERG’s customers include:
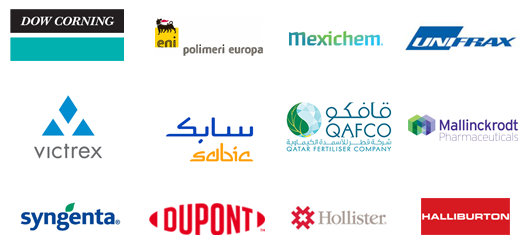
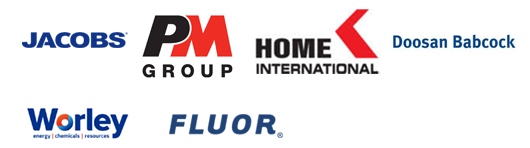
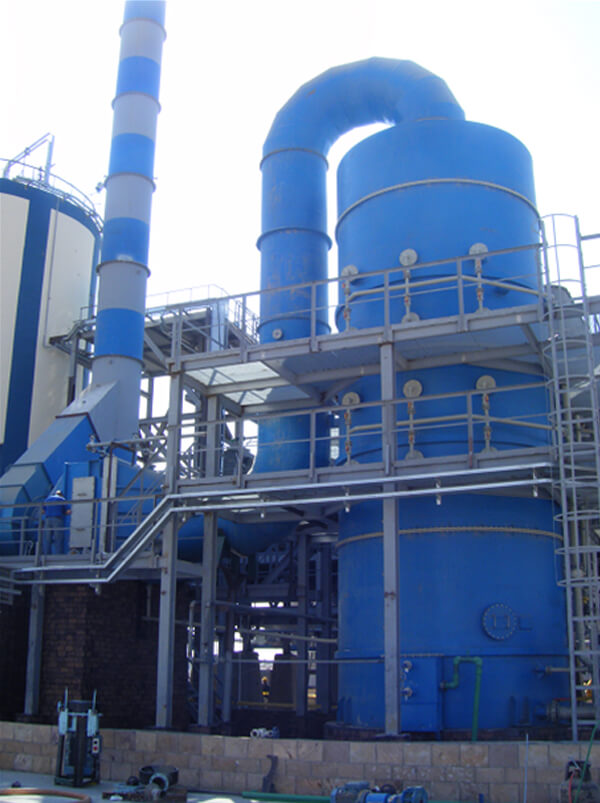
Chemical Plant Air Pollution Treatment
ERG provides a wide variety of air pollution control systems for Chemical production plants. ERG’s purpose-designed scrubbing systems are engineered to suit each application and client’s requirements and are supplied with a process guarantee.
We have reference plants throughout the chemical industry, with sector experience in bulk chemicals, fertilisers, intermediates, fine chemicals, agrochemicals, heat-resistant materials manufacture, speciality chemicals, petrochem and consumer products.
Applications
ERG’s abatement packages are typically installed to treat vents from storage tanks, reactors, vent lines/LEV systems, liquid waste handling, packaging areas and thermal oxidisers. In many cases, a skid-mounted scrubber package is required, though ERG can also arrange site installation and commissioning.
Typical contaminants which we treat include:
- Acid gases – HCl, Cl2, Br2, COS, HCN, SO2, H2S, mercaptans, etc
- Basic gases – NH3, amines, etc
- Silicates – SiO2, H2SiF6, SiF4, SiCl4, etc
- Dust and aerosols – 100 to <1 micron particle sizes – mechanically and chemically generated dust including catalysts, zeolites, PTA, rubber
- VOCs – MEK, methyl chloride, THF, ethyl acetate, acetone, etc
ERG has particular experience treating halogenated semi-metals (BCl3, SiCl4, SiF4, etc) where difficult to handle gelatinous or solid precipitates form on contact with the scrubbing liquor, leading to potential for system blockage.
Download our studies to read further.
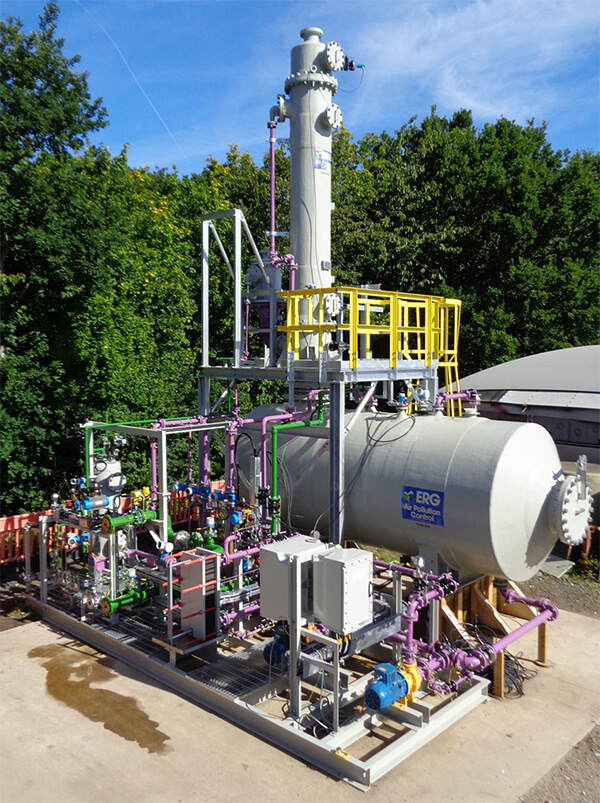
Technologies
Our vent abatement systems are based on one or more of the following technologies. Each package is bespoke: designed and manufactured to the specific project requirements.
- Packed tower scrubbers – for acid gases, basic gases, some dusts, some VOCs
- V-tex® scrubbers – for acid gases, basic gases, some dusts, some VOCs VOCs, and especially suitable to gelatinous hydrolysis products
- Venturi scrubbers – for high concentration or fine dust
- Carbon filters – for VOCs and solvent abatement
- Quench systems – for adiabatically cooling high temperature gas for further wet scrubbing
- Tray scrubbers – typically large flowrate low concentration gases and dusts
- Thermal oxidation – waste solvents and VOC-rich vent gases
- Low temperature DeNOx – for NOx abatement to high efficiency
ERG is skilled at system integration, adding additional abatement techniques from third-party vendors into our systems. Examples include bag filters, ceramic filters, RTOs, SCR/SNCR de-NOx, liquid effluent treatment.
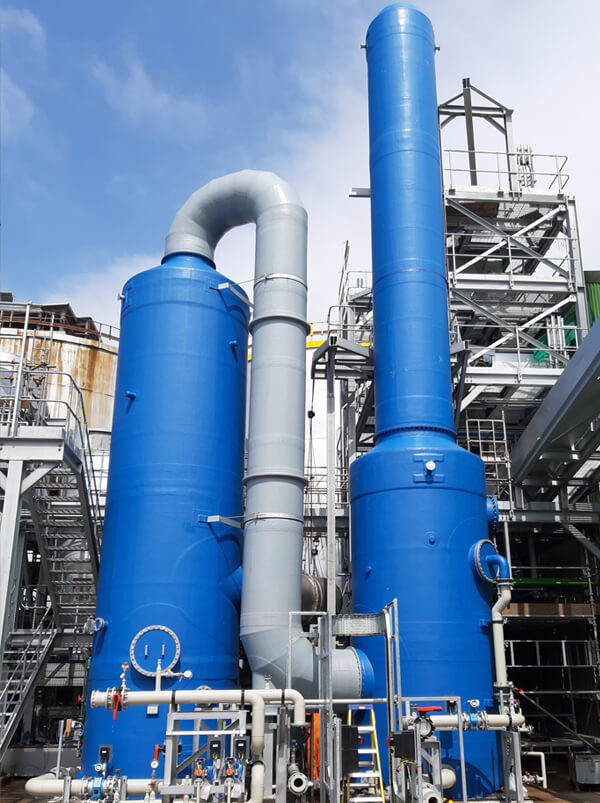
Meeting Exacting Specifications
ERG’s design and project management teams are highly experienced at delivering packaged plant which meets the chemical industry’s needs.
- All design and procurement is managed according to our ISO9001 procedures
- All manufacturing and assembly is to the agreed codes and project specifications, managed through and certified against the project Quality and Inspection & Test Plans.
- All equipment is fully certified and documented in accordance with applicable European Standards, and CE marked accordingly.
- Vessels can be supplied to BS EN 13121, PD 5500 or ASME VIII as appropriate, and packages CE marked to the Pressure Equipment (2014/68/EU) and ATEX (2014/34/EU) Directives depending on the specification requirements.
- Safety in design and operation is our highest priority. We work with the main contractor, designer and end user to ensure the safety case documentation, HAZOP, etc are conducted thoroughly and efficiently.
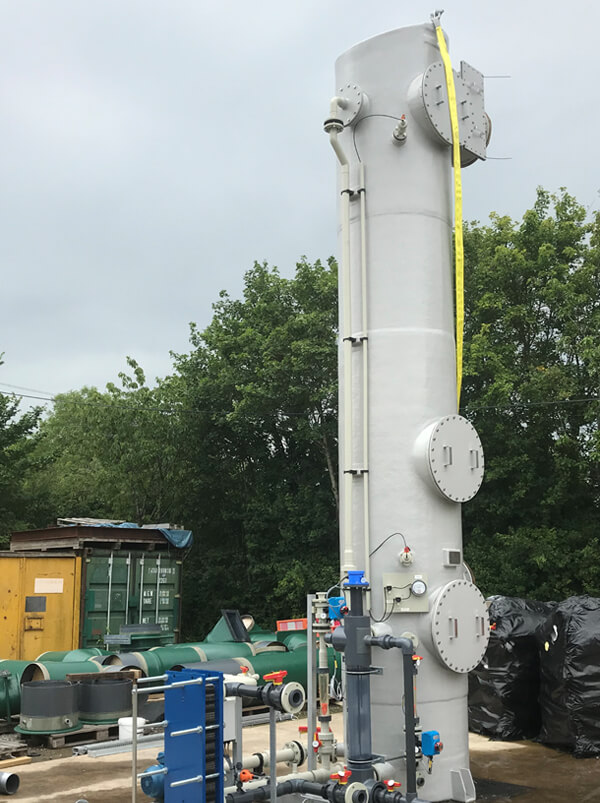
Choice of Materials
Every ERG package has materials selected to match the specification. All systems are mechanically designed for the operating and design pressures (typically ambient ±50-100mbarg, though can be from FV to +40barg) and temperatures (ambient upwards to suit the process). Common materials selections are listed below, though alternatives are available to suit the process requirements.
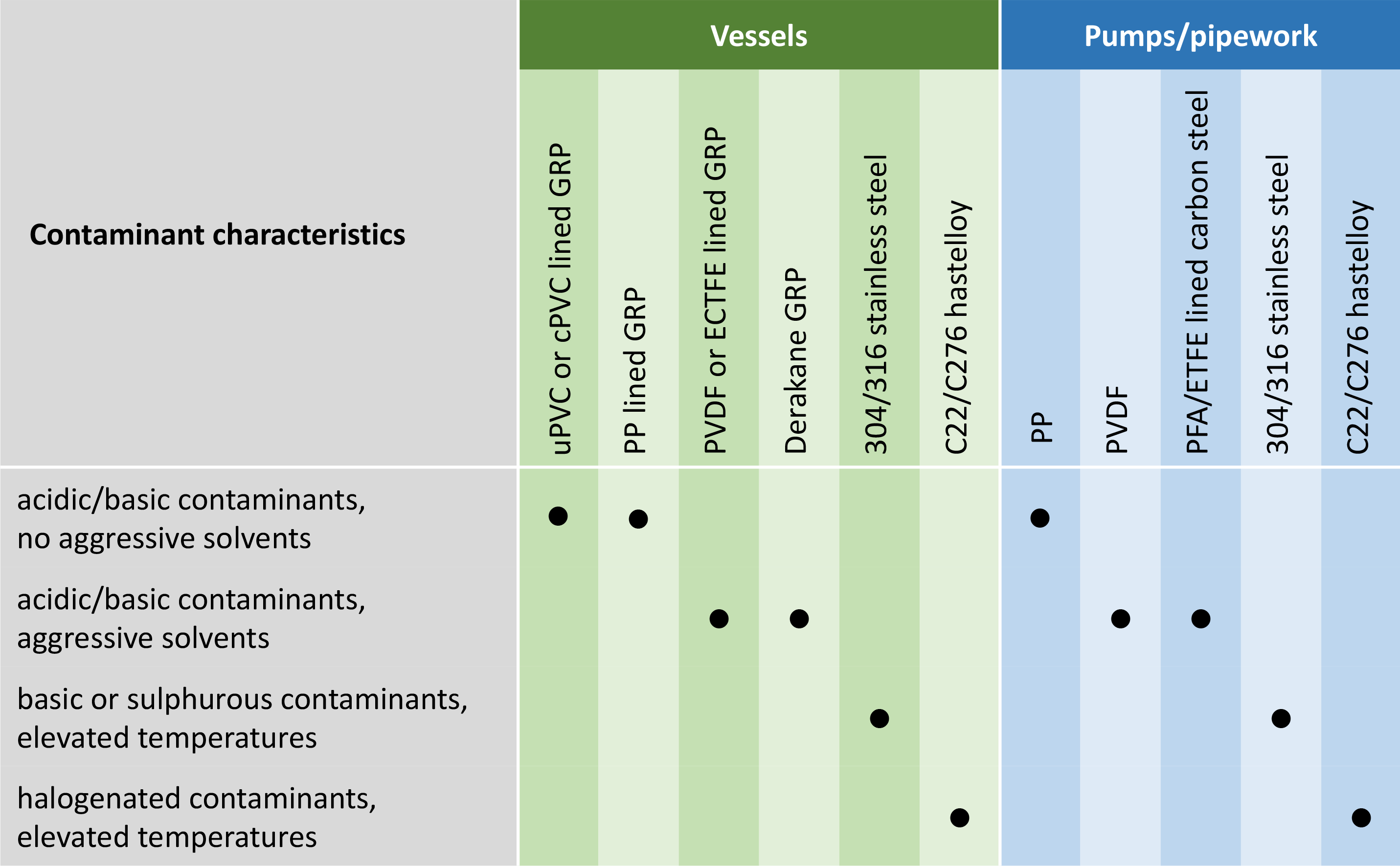
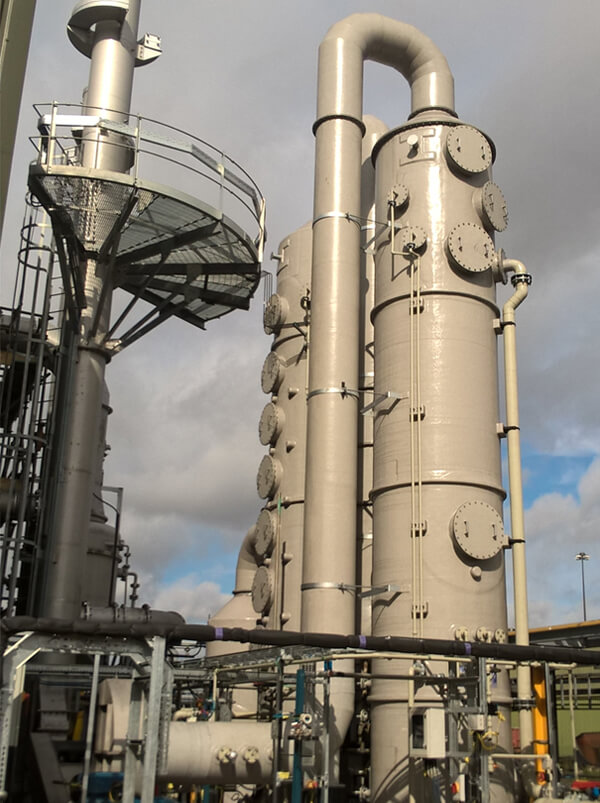
ERG Package Scope of Supply
ERG is a specialised scrubbing supplier. Our typical scope includes:
- Project management including customer design reviews, progress reporting, equipment interface agreement, programme management, site activities co-ordination, documentation packages
- Process design and technical submission – heat & mass balance, P&ID, control philosophy, technical schedules
- Detailed mechanical and electrical design – model and/or package General Arrangement drawings, civils requirements, site wiring details, interface details, off-loading and installation details
- Sub-supplier procurement, quality assurance and expediting – vessels, pipework & valves, pumps, fans, heat exchangers, instrumentation, control panels or local JBs, access steelwork, pressure protection devices
- Package assembly including full pipework and wiring, factory testing, certification
- Delivery
- Installation and commissioning are also available if required – phone support during this phase can be arranged if preferred
Plastic and GRP vessels are manufactured by ERG’s sister company ERG (Plastic Fabrication) Ltd (ergpf.co.uk). Skid assembly and testing are managed at ERG (Plastic Fabrication) Ltd’s facility in West Sussex.
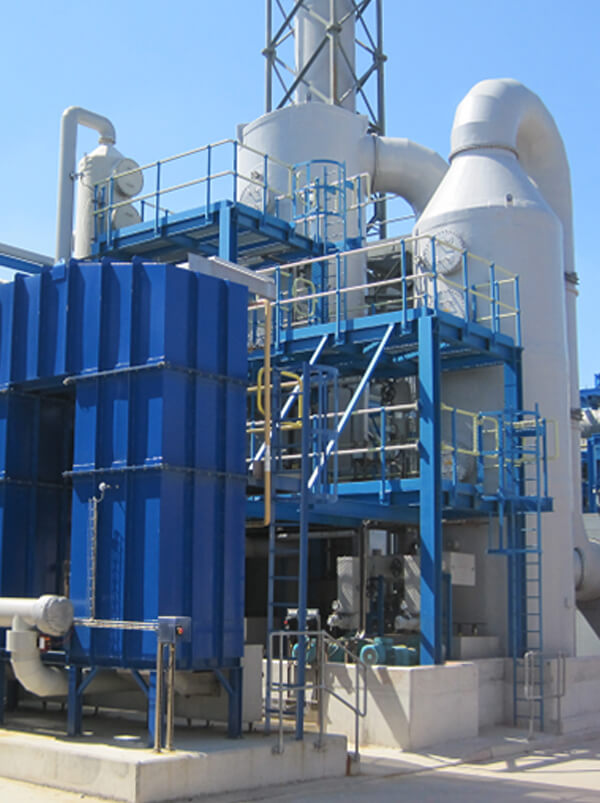
Operational Peace of Mind
- Every ERG abatement package carries a performance guarantee – as an operator you can be sure the equipment will meet the process requirements
- Our standard (12 months) or extended warranty guarantees the mechanical and electrical parts against defects
- And our Maintenance department can assist with routine, shut-down or emergency maintenance
Our Clients
ERG’s customers include:
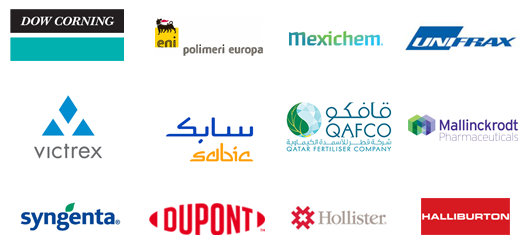
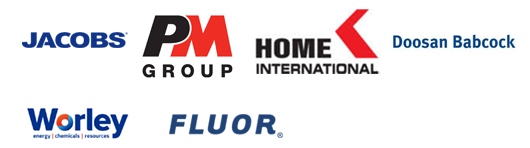
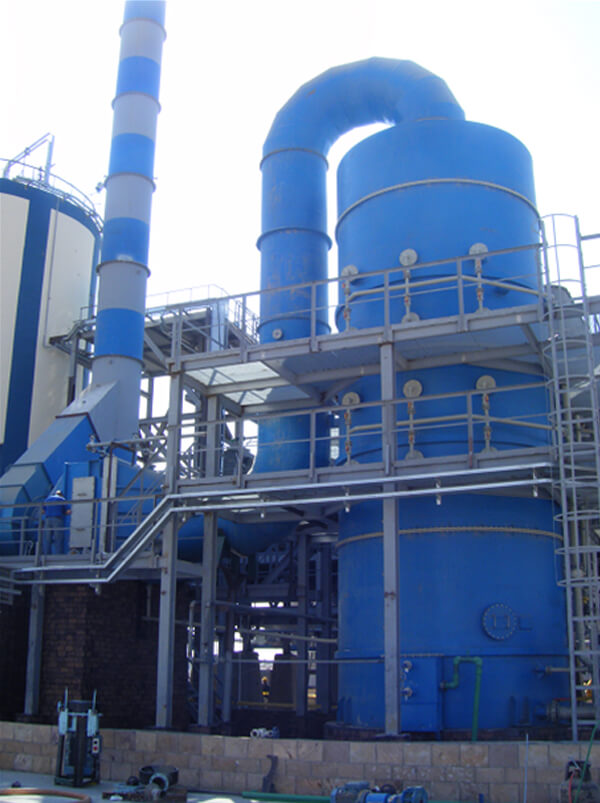